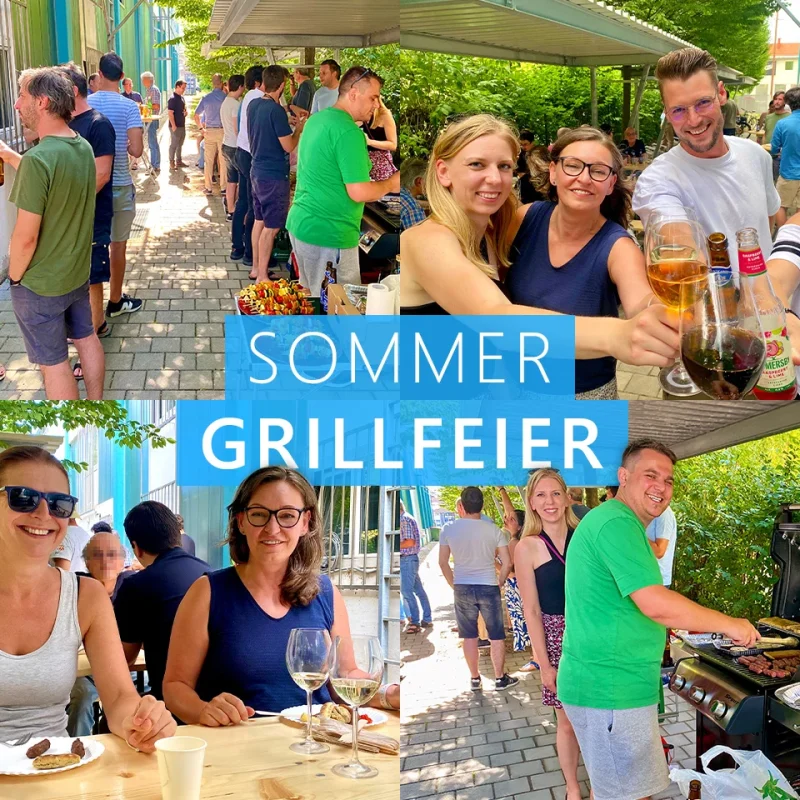
Philipp Seibald
12. November 2023
The OEE value measures the added value of a system and forms the basis for process improvements by identifying production losses and increasing product quality. It can be used to consistently and continuously visualise both the productivity and the losses of a plant at a glance. The application of the OEE method is now the de facto standard in all industrial sectors. For companies implementing lean production, it is an important controlling tool for identifying and counteracting wasted resources.
The OEE figure takes into account the most frequent and most important sources of productivity losses in production and is defined as the product of the following three factors:
Availability losses are technical and organisational system downtimes. For example, malfunctions, set-up times, breaks, lack of resources or maintenance/cleaning.
Performance losses are a reduced production speed and also short downtimes. The best possible speed is required as a reference value when analysing performance. If systems produce different products, the reference speeds can be product-specific.
Quality losses occur when products do not fulfil the specification. Defective products can either be reworked or are scrap. According to the principle of First Time Right, rework is also a loss as unnecessary machine time is consumed.
The OEE value is defined as the product of availability factor, performance factor and quality factor:
This results in a value range between 0 % and 100 %, which indicates the proportion of the planned machine running time that was actually produced in accordance with the quality criteria. This value is usually well below 100 %, as the factors involved can never fully reach 100 %. This clearly shows the limiting factors that need to be worked on.
OEE classifications can be found in the literature as shown in the following diagram.
However, general evaluation schemes are only meaningful to a limited extent, as they do not take important boundary conditions into account. There are industry influences, for example, systems in the pharmaceutical or food industry often have to be sterilised and cleaned. Compared to other industries, this requires more downtime. The order structure also plays a role. Small batch sizes may require frequent set-up and therefore reduce the OEE value.
Like any other key figure, OEE also encourages comparisons. Plant benchmarks, even across different sites, are meaningful if the boundary conditions are comparable, the loss catalogues are standardised and the same determination procedure is used. In our view, the most important thing is to keep an eye on OEE development at key plants.
The OEE method can be used on all different types of systems, regardless of the industry: Single machines, production lines, CNC systems through to batch processes. The method is suitable for discrete, piece-related production as well as for continuously operating systems. While the original focus of application was on series production, we have now also had good experience with small order sizes, right down to batch sizes of one.
It is difficult to use for one-off production, e.g. in special machine construction. For constantly new items, there are usually no or only imprecise planned times, which can distort OEE results. OEE is also rarely used at manual workstations. The manual recording of production processes is an additional effort for the employee and is subject to personal commitment.
Philipp Seibald
Head of Business Development
You need to load content from reCAPTCHA to submit the form. Please note that doing so will share data with third-party providers.
More InformationYou need to load content from Turnstile to submit the form. Please note that doing so will share data with third-party providers.
More Information