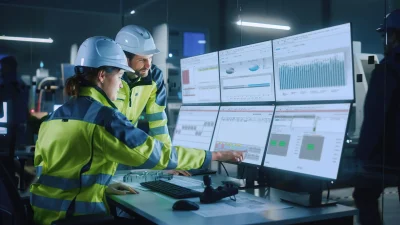
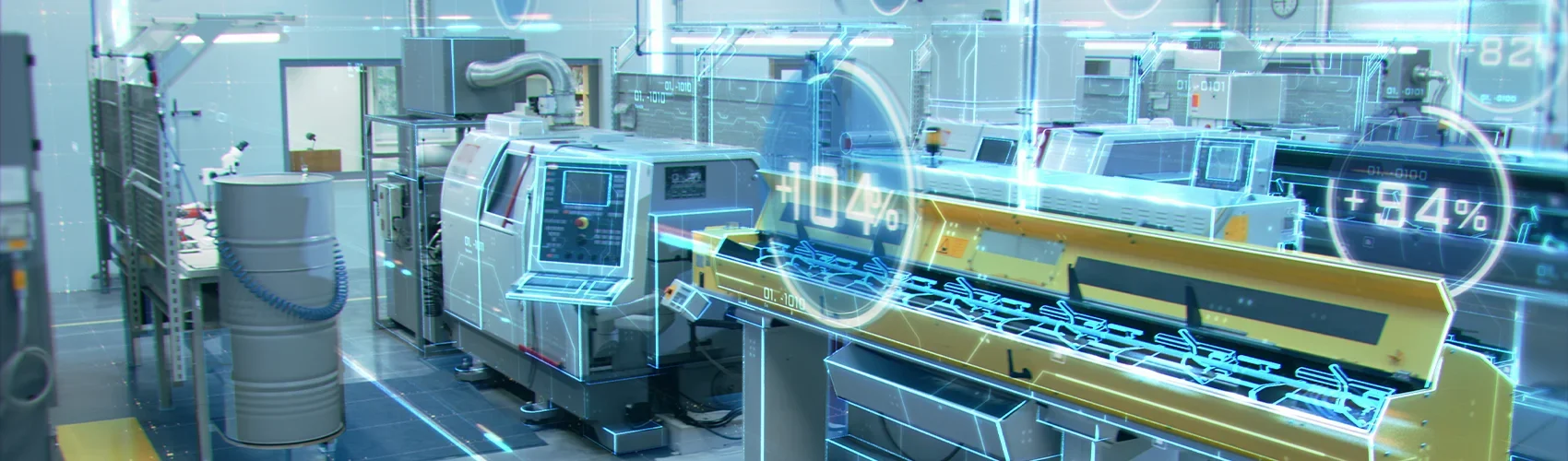
Overview
Solutions
Our Software Solutions
Customer Opinions
Key Industries
-
Steel Industry
The steel industry is a key sector of the global economy and forms the backbone of numerous branches of industry, from the automotive industry to the construction industry. Growing demands for sustainability and efficiency are leading to a transformation that is driving companies to increasingly optimise their processes and production workflows.
-
Pharma Industry
As a key sector, the pharmaceutical industry is essential for global healthcare and drives the development of new therapies with ground-breaking innovations. In the face of increasing regulatory requirements, rising costs and a focus on sustainability, the industry is faced with a balancing act between innovation and efficiency.
-
Food Industry
The food industry in Central Europe plays a central role in the regional economy and ensures the supply of high-quality and safe products. Due to rising wage and energy costs, digitalisation and the associated increase in productivity are increasingly becoming a prerequisite for being able to continue operating production sites in Europe.
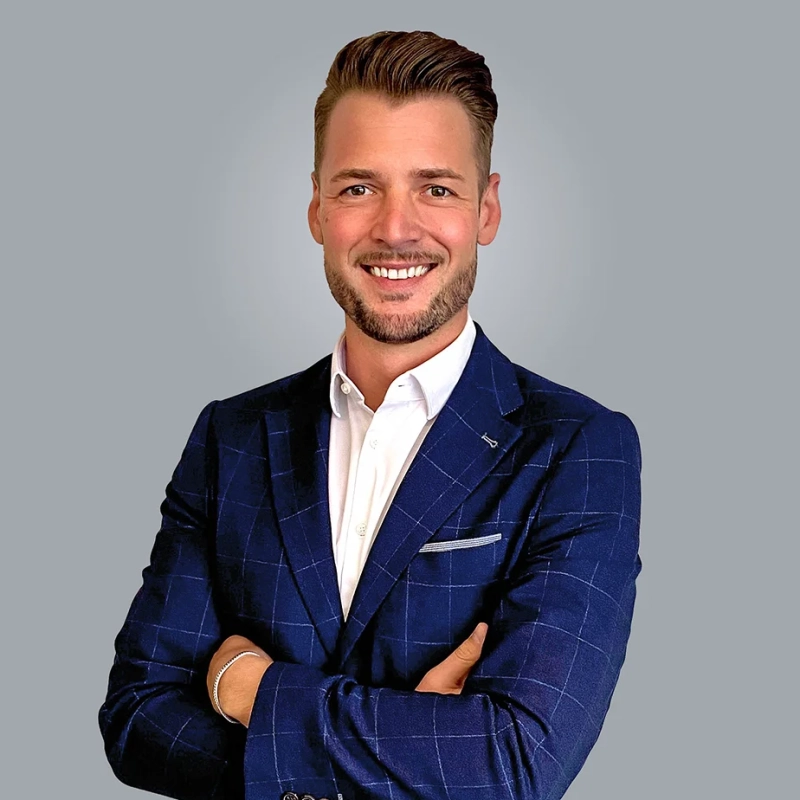
I Will Be Happy to Help You
Philipp Seibald
Head of Business Development