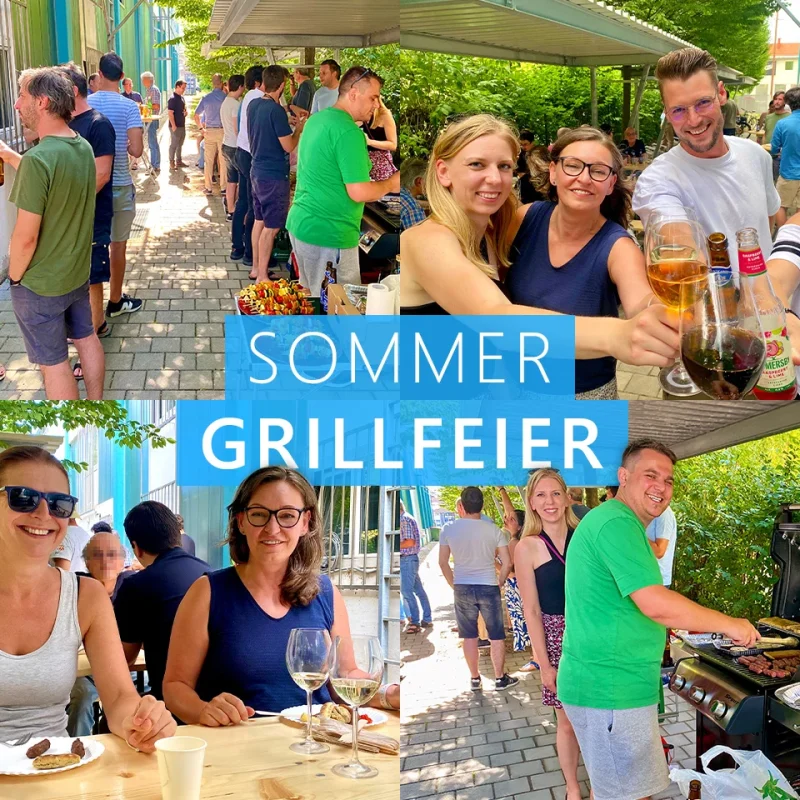
Philipp Seibald
12. November 2023
Der OEE-Wert misst die Wertschöpfung einer Anlage und bildet die Grundlage für Verbesserungen der Prozesse durch die Identifizierung von Produktionsverlusten und Steigerung der Produktqualität. Mit ihm können auf einen Blick sowohl die Produktivität als auch die Verluste einer Anlage konsequent und kontinuierlich dargestellt werden. Die Anwendung der OEE-Methode ist heute De-facto-Standard in allen Industriebereichen. Für Unternehmen, die Lean Production umsetzen, ist sie ein wichtiges Controllinginstrument, mit der Ressourcenverschwendungen aufgedeckt und ihnen entgegengewirkt werden soll.
Die OEE-Kennzahl berücksichtigt die häufigsten und wichtigsten Quellen von Produktivitätsverlusten in der Fertigung und ist als das Produkt der folgenden drei Faktoren definiert:
Verfügbarkeitsverluste sind technische und organisatorische Anlagenstillstände. Beispielsweise Störungen, Rüstzeiten, Pausen, Ressourcenmangel oder Wartung/Reinigung.
Leistungsverluste sind eine reduzierte Produktionsgeschwindigkeit und auch Kurzstillstände. Zur Leistungsbetrachtung wird die bestmögliche Geschwindigkeit als Referenzwert benötigt. Wenn Anlagen unterschiedliche Produkte erzeugen, können die Referenzgeschwindigkeiten produktspezifisch sein.
Qualitätsverluste treten auf, wenn Produkte die Spezifikation nicht erfüllen. Fehlerhafte Produkte können entweder nachgearbeitet werden oder sind Ausschuss. Nach dem Prinzip First Time Right ist auch Nacharbeit ein Verlust, da unnötige Maschinenzeiten verbraucht werden.
Der OEE-Wert ist als Produkt von Verfügbarkeitsfaktor, Leistungsfaktor und Qualitätsfaktor definiert:
Es ergibt sich ein Wertebereich zwischen 0 % und 100 %, der angibt, zu welchem Anteil der geplanten Maschinenlaufzeit tatsächlich den Qualitätskriterien entsprechend produziert wurde. Dieser Wert liegt meist deutlich unter 100 %, da die einfließenden Faktoren 100 % nie völlig erreichen können. So werden die begrenzenden Faktoren deutlich, an denen gearbeitet werden muss.
In der Literatur finden sich OEE-Klassifizierungen wie in der folgenden Abbildung dargestellt.
Allgemeine Bewertungsschemen sind aber nur bedingt aussagekräftig, da sie wichtige Randbedingungen nicht berücksichtigen. Es gibt Brancheneinflüsse, beispielsweise müssen Anlagen in der Pharma- oder Lebensmittelindustrie häufig sterilisiert und gereinigt werden. Gegenüber anderen Branchen sind dadurch vermehrte Stillstände notwendig. Auch spielt die Auftragsstruktur eine Rolle. Kleine Losgrößen erfordern unter Umständen häufiges Rüsten und mindern deshalb den OEE-Wert.
Wie jede andere Kennzahl verleitet auch OEE zu Vergleichen. Anlagenbenchmarks, auch standortübergreifend, sind dann aussagekräftig, wenn die Randbedingungen vergleichbar sind, die Verlustkataloge vereinheitlicht sind und dasselbe Ermittlungsverfahren eingesetzt wird. Das Wichtigste aus unserer Sicht ist, die OEE-Entwicklung an Schlüsselanlagen im Blick zu haben.
Die OEE Methode kann branchenunabhängig an allen unterschiedlichen Anlagentypen eingesetzt werden: Einzelmaschinen, Produktionslinien, CNC-Anlagen bis hin zu Batch-Prozessen. Das Verfahren ist sowohl für die diskrete, stückbezogene Fertigung als auch für kontinuierlich arbeitende Anlagen geeignet. Lag der Einsatzschwerpunkt ursprünglich in der Serienfertigung, haben wir heute auch gute Erfahrungen bei kleinen Auftragsgrößen, bis hin zu Losgröße eins gemacht.
Schwierig ist die Anwendung bei Einmalfertigung, z.B. im Sondermaschinenbau. Für ständig neue Artikel liegen zumeist keine oder nur ungenaue Planzeiten vor, die OEE-Ergebnisse verzerren können. Auch an Handarbeitsplätzen wird OEE eher selten eingesetzt. Die manuelle Aufzeichnung von Fertigungsabläufen ist doch ein Mehraufwand für den Mitarbeiter und unterliegt dem persönlichen Engagement.
Sie müssen den Inhalt von Turnstile laden, um das Formular abzuschicken. Bitte beachten Sie, dass dabei Daten mit Drittanbietern ausgetauscht werden.
Mehr Informationen