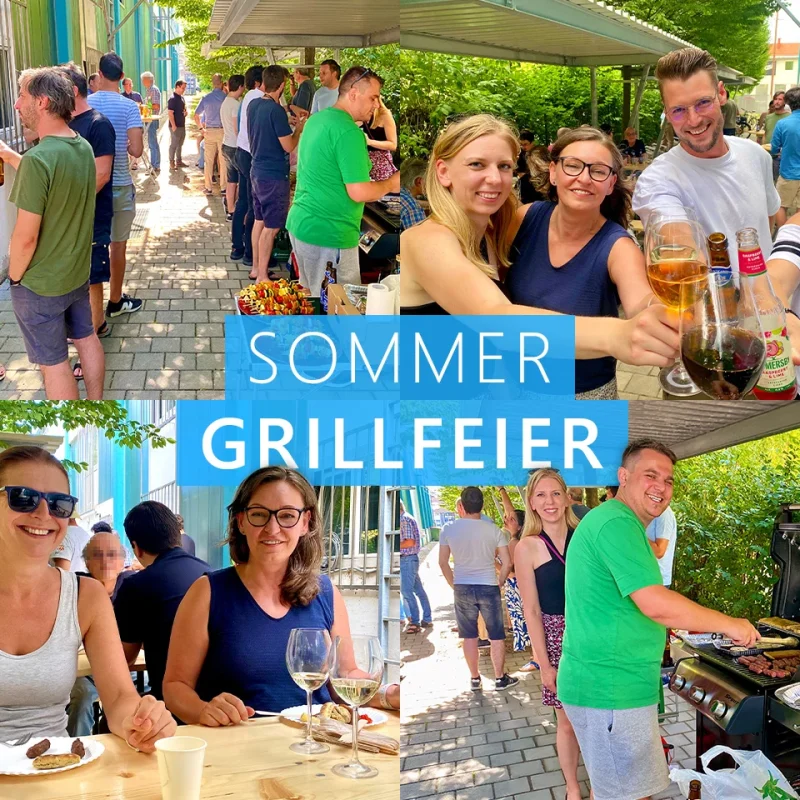
Philipp Seibald
09. August 2023
Mit dem Einsatz von Lean Methoden in Produktionssystemen werden schlanke effiziente Prozesse angestrebt. Lean Production bedeutet, sämtliche Aktivitäten auf den Kunden auszurichten und Werte ohne Verschwendung zu schaffen. Dieses Ziel ist in der Praxis noch nicht erreichbar, doch jeder Schritt in diese Richtung wirkt positiv hinsichtlich:
Zur Einführung von Lean Production empfehlen wir ein Bottom-Up-Vorgehen:
Angefangen an zentralen Anlagen wie Schlüssel- oder Engpassmaschinen werden Verluste/Verschwendungen erhoben, analysiert und stufenweise reduziert. Wenn diese Anlagen die benötigte Performance stabil erreicht haben, können die nachfolgenden Schritte eingeleitet werden. Beispielsweise eine Materialflussoptimierung über eine Wertstromanalyse, Einführung des Pull-Prinzips, Methodik der Fertigungsplanung und Steuerung, etc. Auf oberster Ebene gilt es dann, die unterstützenden Fachbereiche Arbeitsvorbereitung, Qualitätssicherung und Instandhaltung an die Produktionsbedürfnisse auszurichten und zu einem Produktionsteam zusammenzuführen, das ständige Verbesserungen gemeinsam umsetzt.
In allen Einführungsstufen und auch während der operativen Anwendung von Lean dient die OEE-Methode als zentrales Werkzeug. Fokussiert auf Betriebsanlagen wird der erreichte Fortschritt in einem umfassenden Kennzahlensystem dargestellt. Lean Management setzt in hohem Maß auf Visualisierung. Auch hier bietet OEE interessante Möglichkeiten, Anlagenbediener und Führungskräfte wirksam zu unterstützen.
Die OEE Methode kann branchenunabhängig an allen unterschiedlichen Anlagentypen eingesetzt werden: Einzelmaschinen, Produktionslinien, CNC-Anlagen bis hin zu Batch-Prozessen. Das Verfahren ist sowohl für die diskrete, stückbezogene Fertigung als auch für kontinuierlich arbeitende Anlagen geeignet. Lag der Einsatzschwerpunkt ursprünglich in der Serienfertigung, haben wir heute auch gute Erfahrungen bei kleinen Auftragsgrößen, bis hin zu Losgröße eins gemacht.
Schwierig ist die Anwendung bei Einmalfertigung, z.B. im Sondermaschinenbau. Für ständig neue Artikel liegen zumeist keine oder nur ungenaue Planzeiten vor, die OEE-Ergebnisse verzerren können. Auch an Handarbeitsplätzen wird OEE eher selten eingesetzt. Die manuelle Aufzeichnung von Fertigungsabläufen ist doch ein Mehraufwand für den Mitarbeiter und unterliegt dem persönlichen Engagement.
OEE ist ein offener Standard zur Produktivitätsermittlung. In einem festgelegten Ermittlungsverfahren können Sie Ihre konkreten Verlustursachen frei definieren und einzelnen Verlustgruppen zuordnen. Betrachten wir eine Anlage durchgängig über einen beliebigen Zeitraum (24*7), dann gibt es 4 unterschiedliche Verlustgruppen:
Nutzungsverluste sind Stillstände, die im Wesentlichen die geplante produktionsfreie Zeit umfassen (gemäß Ihren Schicht- und Zeitmodellen). Beispiele sind Wochenende/Feiertag, Betriebsurlaub oder freie Schichten. Auch Stillstände bedingt durch Auftragsmangel oder höhere Gewalt sollten als Nutzungsverluste angelegt werden.
Verfügbarkeitsverluste sind technische und organisatorische Anlagenstillstände. Beispielsweise Störungen, Rüstzeiten, Pausen, Ressourcenmangel oder Wartung/Reinigung.
Leistungsverluste sind eine reduzierte Produktionsgeschwindigkeit und auch Kurzstillstände. Zur Leistungsbetrachtung wird die bestmögliche Geschwindigkeit als Referenzwert benötigt. Wenn Anlagen unterschiedliche Produkte erzeugen, können die Referenzgeschwindigkeiten produktspezifisch sein.
Qualitätsverluste treten auf, wenn Produkte die Spezifikation nicht erfüllen. Fehlerhafte Produkte können entweder nachgearbeitet werden oder sind Ausschuss. Nach dem Prinzip First Time Right ist auch Nacharbeit ein Verlust, da unnötige Maschinenzeiten verbraucht werden.
Anhand der 4 Verlustgruppen werden Verlustfaktoren ermittelt und daraus die Produktivitätskennzahlen OEE und TEEP (Total Effective Equipment Productivity) gebildet.
Warum nun OEE und TEEP? Wie oben ersichtlich, schließt die OEE-Kennzahl alle Nutzungsverluste aus und gibt an, wie produktiv die Anlage innerhalb der geplanten Produktionszeit gelaufen ist. Sie ist deshalb die entscheidende Kennzahl für das Produktionsteam. Die TEEP-Kennzahl umfasst alle Verlustgruppen und ist für das Management interessant, da in den Nutzungsverlusten Kapazitätsreserven erkennbar sind.
Mit den OEE- und TEEP-Kennzahlen lässt sich die Entwicklung der Anlagenproduktivität verlässlich und gut darstellen. Soweit alles im grünen Bereich liegt, brauchen wir nicht mehr. Wenn jedoch das angestrebte Niveau nicht erreicht wird oder kurzfristige Einbrüche auftreten, dann interessieren uns die Gründe dafür. Weiterführende Analysen und Kennzahlen sollten deshalb in jedem OEE-System inkludiert sein, um die Verlustursachen zu erkennen. Dazu einige Beispiele:
In der Literatur finden sich OEE-Klassifizierungen wie in der folgenden Abbildung dargestellt:
Allgemeine Bewertungsschemen sind aus unserer Sicht nur bedingt aussagekräftig, da sie wichtige Randbedingungen nicht berücksichtigen. Es gibt Brancheneinflüsse, beispielsweise müssen Anlagen in der Pharma- oder Lebensmittelindustrie häufig sterilisiert und gereinigt werden. Gegenüber anderen Branchen sind dadurch vermehrte Stillstände notwendig. Auch spielt die Auftragsstruktur eine Rolle. Kleine Losgrößen erfordern u.U. häufiges Rüsten und mindern deshalb den OEE-Wert.
Wie jede andere Kennzahl verleitet auch OEE zu Vergleichen. Anlagenbenchmarks, auch standortübergreifend, sind dann aussagekräftig, wenn die Randbedingungen vergleichbar sind, die Verlustkataloge vereinheitlicht sind und dasselbe Ermittlungsverfahren eingesetzt wird. Das Wichtigste aus unserer Sicht ist, die OEE-Entwicklung an Schlüsselanlagen im Blick zu haben.
War ursprünglich die OEE-Methode als Werkzeug für das Produktionsteam gedacht, so hat sich der Anwenderkreis auch auf andere Bereiche ausgeweitet. OEE wurde zu einem zentralen Informations- und Kennzahlensystem im Unternehmen. Neben dem Produktionsmanagement unterstützt OEE folgende Benutzergruppen:
Durch schichtbezogene, möglichst zeitnahe Informationen über Anlagenzustände, Auftragsfortschritt oder Schichtleistung werden Anlagenbediener im Schichtbetrieb und in der Schichtübergabe unterstützt. Die Visualisierung wichtiger Produktionsparameter fördert das Prozessverständnis und hilft den Mitarbeitern, die Planvorgaben zu erfüllen.
Aufgetretene Anlagenstörungen können zeitnah gemeldet und so rasche Reparaturmaßnahmen eingeleitet werden. Die Entwicklung der technischen Anlagenverfügbarkeit ist ein wichtiger Leistungsindikator der Instandhaltung und dient zur Optimierung der Instandhaltungsstrategien und zum Aufbau eines Instandhaltungscontrollings.
Durch genaue Kenntnisse über Fehlerursachen und Häufigkeiten können Prüfvorschriften angepasst und Maßnahmen zur Fehlervermeidung umgesetzt werden.
Häufig sehen wir, dass in eingesetzten Planungssystemen die Planzeiten veraltet sind und nicht mehr der Realität entsprechen. Anhand der Ergebnisdaten aus OEE können produktspezifische Planzeiten an einzelnen Anlagen laufend optimiert und so die Planungsgenauigkeit und Nachkalkulation verbessert werden.
Leistungsauswertungen und Schwachstellenanalysen sind eine Fundgrube für TPM-Maßnahmen und KVP-Projekte. Dazu ist es wichtig, die zuständigen Mitarbeiter in regelmäßige Ergebnisbesprechungen einzubinden, um wiederkehrende Probleme in Verbesserungsprojekte überzuleiten.
Auch auf Managementebene wird OEE zusehends wichtiger. Verdichtete Informationen bieten den raschen Blick auf die Entwicklung im Betrieb. Der Grad der Kapazitätsnutzung der Anlagen ist eine wichtige Hilfe bei Neuinvestitionen, um teure Überkapazitäten zu vermeiden. Im Rahmen der innerbetrieblichen Zielvereinbarung dienen OEE Ergebnisse auch dazu, messbare Ziele für einzelne Fachbereiche aufzustellen.
Gelegentlich werden die OEE-Kennzahlen noch rein manuell ermittelt. Dazu werden vom Anlagenbediener erzeugte Mengen und Produktionsereignisse in Formulare eingetragen und daraus die Ermittlungen gemacht. Häufig wird auch Excel eingesetzt und unterstützt die Berechnungen und grafische Ergebnisdarstellung. Automatisierte Verfahren erfassen über eine Maschinenanbindung alle relevanten Ereignisse automatisch und liefern die Ergebnisse.
Die unterschiedlichen Methoden werden in den Stufen „Erhebung der Basisdaten – Berechnungen – Ergebnisdarstellung“ ersichtlich und können anhand folgender Kriterien beurteilt werden:
Dieser entsteht durch Ausfüllen von Formlaren, manuellen Berechnungen bzw. Dateneingabe in ein Berechnungssystem. Bei einem automatisierten Verfahren ist der Gesamtaufwand vernachlässigbar. Die Mitarbeiter werden von lästiger Routinearbeit entlastet und gewinnen Zeit für die viel wichtigere Problemanalyse und für Verbesserungen. Das manuelle Verfahren sollte nur temporär für Übungszwecke verwendet werden, um Mitarbeiter mit der Methode vertraut zu machen. Bei wenigen Anlagen kann ein halbautomatisches Verfahren ausreichend sein. Ab einer gewissen Größenordnung (erfahrungsgemäß >3 Anlagen) empfehlen wir ein automatisiertes System. Die etwas höhere Anfangsinvestition wird durch den geringen Personalaufwand rasch kompensiert. Ein automatisches Verfahren bietet noch weitere Vorteile:
Bei Verfahren, wo Basisdaten vom Mitarbeiter erhoben werden, liegen die OEE-Ergebnisse in der Regel 10–15 % über der Realität. Grund dafür ist, dass in hektischen Betriebsphasen die Aufzeichnungen/Eingaben oft vergessen werden. Insbesondere sind versteckte Verluste wie Kurzstillstände oder Leistungsschwankungen mit manuellen Verfahren kaum erfassbar.
Automatisierte Verfahren bieten weiters die Möglichkeit, Ergebnisse laufend und in Echtzeit anzuzeigen. Dadurch werden Anlagenbediener im Schichtbetrieb optimal unterstützt. Auch Produktionsverantwortliche profitieren von Echtzeitinformationen über Auftragsfortschritt, Schichtleistung oder Maschinenzustände. Das OEE System kann darüber hinaus Visualisierungssysteme in der Produktion (Andon Board) mit aktuellen Daten versorgen.
Weiterführende Informationen über unser OEE-Produkt OEE Analyser finden Sie hier: Maschinendatenerfassung (MDE)
OEE liefert alle wichtigen Performanceindikatoren der Anlagen und dient dazu, Schwachstellen zu erkennen und zu beseitigen. Der größte Nutzen wird dann erzielt, wenn OEE in eine umfassende Verbesserungsorganisation eingebettet wird. Der Aufbau eines nachhaltigen OEE-Managements erstreckt sich über folgende Bereiche:
Ausgangspunkt ist die Wahl des Ermittlungsverfahrens. Abhängig davon wird die IT-Landschaft mit Hardware, Vernetzung, Software und Anlagenschnittstellen ausgelegt. Beim Aufbau der Stammdaten und der Verlustkataloge sollten Sie auf Durchgängigkeit achten. Technische Störungsgründe sind zumeist anlagenspezifisch, organisatorische Stillstände und Nutzungsverluste können Sie vereinheitlichen, um realistische Benchmarks zu ermöglichen.
Mitarbeiter für OEE zu gewinnen ist oft nicht einfach. Anfängliche Befürchtungen hinsichtlich Überwachung und Kontrolle können zu ablehnenden Reaktionen führen. Um Mitarbeitern diese Ängste zu nehmen, empfehlen wir ausreichende Schulungsmaßnahmen und eine laufende Begleitung. In unserem Kundenkreis sehen wir, dass reservierte Einstellungen seitens der Mitarbeiter schon kurze Zeit nach Anwendung in eine positive Richtung drehen. OEE wird dann zum begleitenden Tool, um Abläufe an der Maschine besser zu verstehen und erbrachte Leistungen objektiv zu belegen.
In manchen Betrieben mit Prämiensystemen fließen OEE-Ergebnisse in die Prämienermittlung ein. Hier empfehlen wir nur jene OEE-Parameter heranzuziehen, die der Mitarbeiter auch wirklich beeinflussen kann.
OEE braucht personelle Zuständigkeiten. Wir empfehlen die Rolle eines OEE-Koordinators, die üblicherweise von Produktionsleitung, Lean-Management oder von TPM/KVP-Koordinatoren übernommen wird. Der OEE-Koordinator ist für die Pflege des OEE-Systems, wie Erweiterung der Stammdaten oder Optimierung der Sollvorgaben, zuständig. Eine zentrale Aufgabe ist die Organisation von regelmäßigen Meetings. Beispielsweise tägliche und wöchentliche Meetings im operativen Bereich und Monatsmeetings auf Managementebene. Dabei werden die Ergebnisse im Team vorgestellt und Abweichungen analysiert. Bei wiederkehrenden Problemen ist der OEE-Koordinator für die Auslösung von entsprechenden Maßnahmen wie Mitarbeiterschulung, Ablaufänderungen oder technische Verbesserungen zuständig.
Für den langfristigen Erfolg ist die Unterstützung durch das Management wichtig. Am besten gelingt dies durch die Aufbereitung verdichteter Daten aus dem OEE-System für technische Geschäftsführer und Werksleiter. Im Controlling können die technischen Kennzahlen einfach in Finanzzahlen und Kostenbewertungen übersetzt werden. OEE-Managementinformationen dienen als Entscheidungsbasis für erforderliche Investitionen in den Verbesserungsprozess.
Jede Reduktion von Verlusten bewirkt eine Steigerung der OEE-Kennzahl. Die Auswirkungen an einer Anlage sind in der Grafik oben dargestellt.
Weniger Verluste, beispielsweise ein schnelleres Rüsten, verkürzen die Durchlaufzeiten der Aufträge. Dadurch können Sie rascher und flexibler liefern. Eine Reduktion der Durchlaufzeiten vermindert die stückbezogenen Fertigungskosten entsprechend.
Bei guter Auftragslage kann nach Steigerung der OEE mit denselben Ressourcen mehr produziert und verkauft werden. Dies gilt insbesondere für Engpassanlagen. An Anlagen, die nicht Engpass sind, kann durch eine Anpassung der geplanten Betriebszeit die Gefahr von Überbeständen in der Fertigung vermeiden werden.
Die Erfolge durch OEE sind in der Praxis sehr unterschiedlich, abhängig von der jeweiligen Ausgangslage und den Rahmenbedingungen. Hier einige Beispiele aus unserem Kundenkreis:
Die Digitale Produktion verfolgt das Ziel, Prozesse besser zu verstehen, zu steuern und zu optimieren. Schlüsselaufgaben dabei sind die Datenerfassung in der gesamten Prozesskette, Datenanalysen für unterschiedliche Benutzergruppen sowie die Einführung optimierter Steuerungsverfahren. Die Ausgangslage ist in jedem Unternehmen anders: unterschiedliche Steuerungen und IT-Systeme in den einzelnen Bereichen erfordern einen individuellen Plan zur Zielerreichung.
OEE spielt eine zentrale Rolle in der Digitalen Produktion. Insbesondere automatisierte OEE-Systeme können als Einstieg in das umfassende Thema dienen und bieten vielfach Erweiterungsmöglichkeiten in Richtung MES-Lösung (Manufacturing Execution System).
Dieses White Paper basiert auf über 25 Jahren OEE Erfahrung in unterschiedlichsten Industriebetrieben. An Betriebsanlagen, wo Wertschöpfung im Unternehmen erfolgt, ist OEE aus meiner Sicht ein Muss, um die Mitarbeiter zu unterstützen und die Kapazitätsnutzung auf Managementebene präzise und verständlich darzustellen.
Ich hoffe, Sie konnten einige Empfehlungen und Tipps für Ihre Praxis mitnehmen. Wenn Sie Fragen, Anregungen oder Kritik haben, so stehen wir Ihnen gerne zur Verfügung. Sie erreichen uns unter: sales@gamed.com